Intro
Interest in MMC and modular housing has hit a peak not seen for several decades as decision makers begin to realise that offsite solutions deliver homes faster, more sustainably, and to a higher level of quality than traditional construction. An eruption of investment in the sector has seen innovative volumetric manufacturers such as Ilke Homes, TopHat, Laing O’Rourke, and Legal & General Modular Homes embark on major housing roll outs across the country.
The world of volumetric construction has moved on considerably from the days of leaky prefabricated buildings. For example, Ilke Homes’ solution harnesses artificial intelligence, robotics, and digital design, to create precision-engineered incredibly well insulated homes, which are kitted out with the latest low-carbon technologies, including air source heat pumps, solar panels and battery storage technology. The manufacturer secured £60m of investment in 2021, which it will use to ramp up its modular housing output, with plans to deliver 10,000 homes over the next five years. Its factory in Knaresborough opened in 2018 and is expected to be operating at full capacity by 2023.
Also experiencing strong demand, TopHat revealed plans last month to open Europe's largest modular housing factory, the size of 11 football pitches, in Northamptonshire in 2023. Located in Corby, the facility will be the firm’s second in the East Midlands, able to manufacture and distribute 4,000 homes a year, or one house per hour, when it reaches full production.
Meanwhile, L&G Modular Homes’ pipeline of homes has grown to include sites in Selby, Bristol, North Horsham, Warminster, and two sites in Kent, with land opportunities for the delivery of several thousand more homes also advancing.
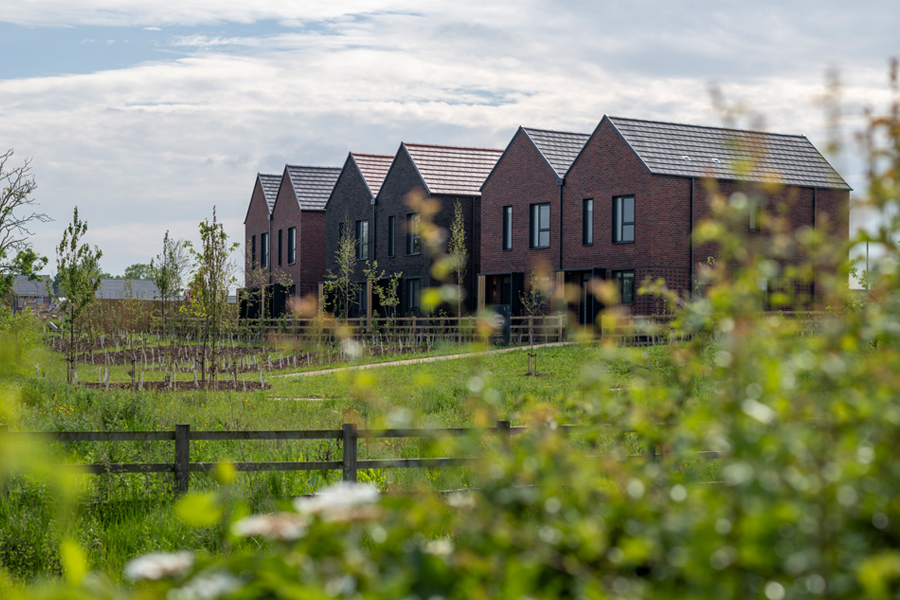
Right time?
A range of societal and economic factors have built the case for more high tech MMC start-ups with factories in the UK. The government has committed to building 300,000 homes a year, a goal it has consistently fallen short on. Just 216,000 new homes were supplied in 2020/21, fewer than the 243,000 supplied in the previous year, in part because of disruption caused by COVID. A key incentive of switching to modular housing is the reduction in construction time and factory-based production has been reported to reduce this by up to 30%. A recent report penned by Mark Farmer, independent MMC adviser to the government, called for Whitehall to make offsite the core of its housing agenda, targeting the delivery of 75,000 new-build modular homes every year by 2030.
The ongoing impacts of the pandemic, high materials and labour costs, and the government’s ‘Build Build Build’ pledges all underline the case for MMC as developers look for solutions to deliver housing quickly. Affordable housing is a key area of concern in the UK. According to a recent report by the charity Shelter, at least 1.2m homes are needed to accommodate younger families unable to afford ownership or struggling in an expensive and insecure rental market.
As a result, local authorities increasingly see modular as a means to unlock residential sites, and deliver homes more cost effectively and, crucially, at a consistently high level of quality. Homes England, the government’s housing delivery agency, now requires housing associations looking to sign strategic partnership deals to build affordable homes to commit to using MMC to build out at least 25% of their pipeline.
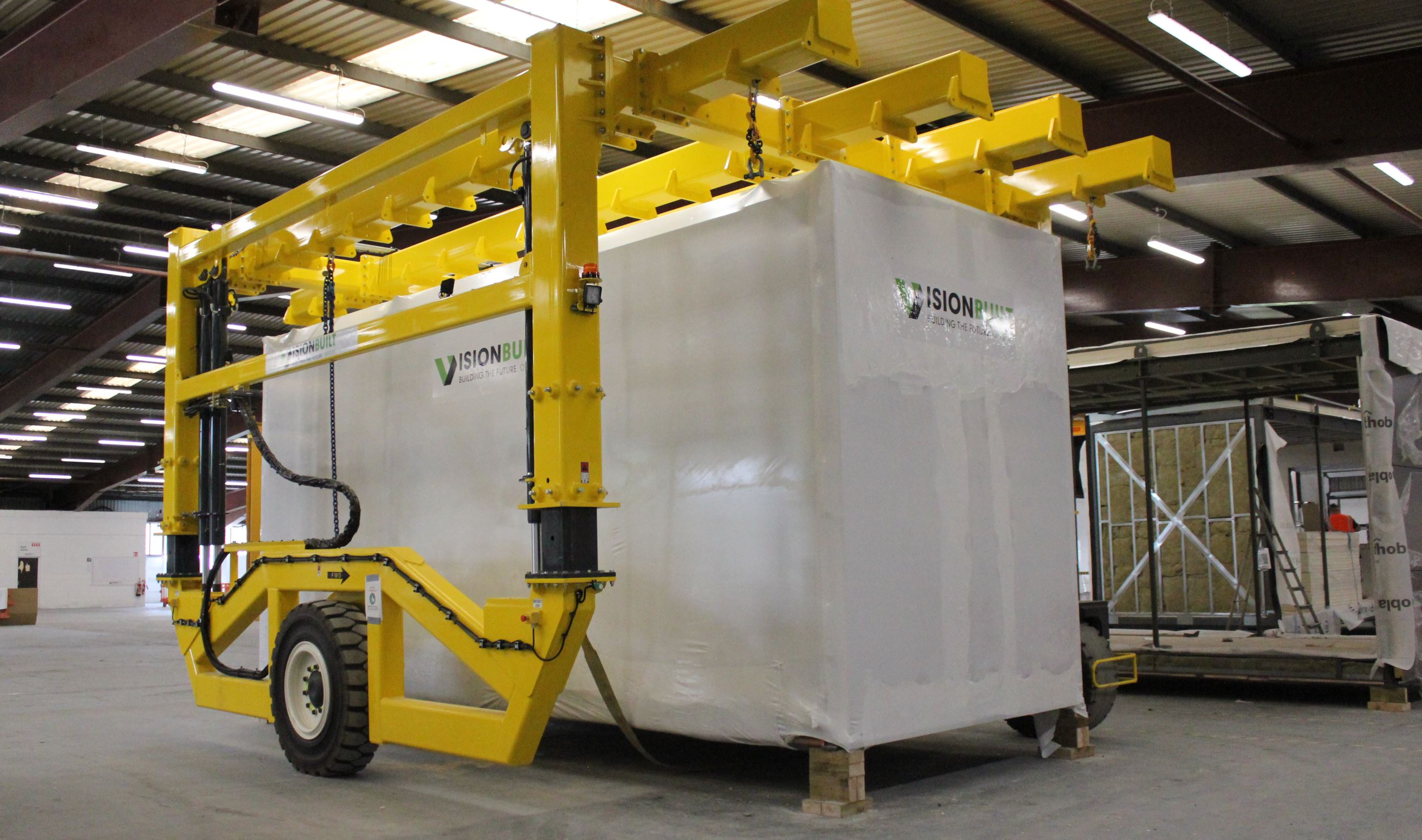
Sustainable sense
The climate emergency has galvanised positive action across the construction sector and investors focused on the environmental, social and governance (ESG) agenda increasingly see MMC and modular as a mechanism for securing their long-term objectives. The latest research by academics from the University of Cambridge and Edinburgh Napier University found that modular schemes can cut embodied carbon by over 40% compared to traditional construction. The two residential tower developments examined in the study had 41 per cent and 45 per cent less embodied carbon than equivalent buildings built traditionally using reinforced concrete, saving a total 8,000 tonnes of embodied carbon emissions during construction.
Precision manufacturing in a factory environment and the use of high-grade insulation materials also enables volumetric homes to achieve a better energy performance than traditionally-built homes. Recent examples include the delivery of four zero carbon homes in the London Borough of Greenwich by Ilke Homes. The manufacturer also entered into a partnership with Octopus Energy last month to deliver the UK's first homes that will guarantee zero energy bills for residents. Furthermore, a 153-home scheme in Kent by L&G Modular Homes is designed to achieve an Energy Performance Certificate ‘A’ rating, placing them in the top 1% of homes for energy efficiency in England and Wales.
With UK inflation hitting a 40-year high, build costs skyrocketing and lingering supply chain impacts from the pandemic and Brexit, it’s easy to see why MMC and modular is an increasingly attractive option for housing delivery. Among other things, it has resulted in the creation of new procurement frameworks, tenders and client organisations tasked with increasing the use of modular in programmes.
Last December saw the launch of the dedicated trade body Make UK Modular, represented by five category 1 modular firms, which outlined plans to invest over £500 million and deliver over 75,000 modular homes by the end of the decade. Backed by parent manufacturing trade body Make UK, the organisation aims to convince the government of the key role for modular to help meet its ambitions around housing demand, net zero, levelling up and a post-Brexit ‘global Britain’.
Warning signs
The resurgence of interest in MMC and modular housing is great news, but if this is to become the decade when offsite goes mainstream, the sector needs clearer direction and support. The recent collapse of the offsite specialist Caledonian Modular, which went into administration in March before being bought by JRL Group, and of House, the modular arm of Urban Splash, highlighted the fragility of a sector forced to also deal with the impacts of a pandemic, rising inflation and a war in Ukraine.
Unlike traditional housebuilders, manufacturers must commit significant amounts of capital to get operations up and running and greater financial and policy support can help bring down costs that act as a barrier to entry to many start-ups. However, the construction industry, lending companies and government regulators have been slow to update policies and practices to make way for the modular industry’s growth. It’s over a year since Rishi Sunak unveiled plans for a new taskforce, backed by £10m of government funding, designed to stimulate housebuilding using MMC, but details of its scope and objectives have still to emerge. Meanwhile, more land needs to be made available for offsite housing schemes, Make UK Modular is currently exploring the different levers it can pull, such as joint bidding on developable land.
Modular responds to several key challenges faced by housebuilding, around speed, sustainability and quality, the coming months will determine if this pioneering approach can reach its true potential.
Our work at KOPE originally grew from our activities in the volumetric modular housing space and the needs across the sector from a technology point of view are clear. Our work is focused on enabling these new house builders to design and fabricate consistently high quality products that give their tenants the best possible living experience. As the industry continues it's journey, our efforts will focus on connecting new and exciting housing designs directly to manufacturing processes and delivering a consistent, easy to use platform for offsite to flourish.