Intro
Modular techniques have been used to deliver some of the world’s most innovative and interesting buildings, let’s explore the projects rewriting the rules of construction for the digital age…
Precision engineering, careful quality control, faster delivery on site and reduced waste all define the modular approach to construction and organisations the world over are exploiting these characteristics to respond to a range of pressing challenges.
Whether it’s the first ‘micro living’ apartments designed to boost housing delivery; emergency hospitals built in record time, or homes that float on water in an era of sea level rise, innovative MMC techniques are proving their value and versatility in many scenarios and settings…
Rapid response
When natural disasters strike it demands a fast and organised response and the efficiency of modular construction has been harnessed in locations worldwide to rapidly erect emergency shelter and healthcare facilities.
Skyrocketing illness and death rates in China triggered by the onset of the COVID-19 pandemic in early 2020, led to the unimaginably fast erection of a modular hospital in the now infamous Wuhan district.
The temporary 1,000-bed hospital was built, by China State Construction 3rd Bureau Engineering (CSCEC-3), in a record 10 days, where a project that large might typically take 6 months to design and up to 3 more years to build. Rising to the challenge, the architect CITIC General Institute of Architectural Design and Research, submitted a ground-levelling scheme in 5 hours, finalised a design plan in 24 hours, and delivered construction drawings in 60 hours.
A concurrent approach to construction saw procedures for design, construction, scheme modification, and adjustment completed in parallel. Digital design in BIM enabled the speedy visualisation, iteration and sharing of data in real time to accelerate delivery. In another innovative use of technology, the entire construction process was live streamed to tens of millions of Chinese viewers, who cheered on workers as they tackled the mammoth task.
The UK government’s 2030 deadline to build 40 new hospitals will demand a similar intense response from construction firms, making modular an attractive option to pursue.
Soaring ambition
Modular isn’t just quick, sustainable and low on waste, modern advances enable it to rival even the world’s tallest high rises built by traditional methods.
At an eye-watering 140m tall, Clement Canopy in Singapore is the world’s tallest modular tower. The luxury housing development, designed by ADDP Architects and constructed by Bouygues Bâtiment International, contains 505 apartments constructed from 1,899 pre-finished concrete modules.
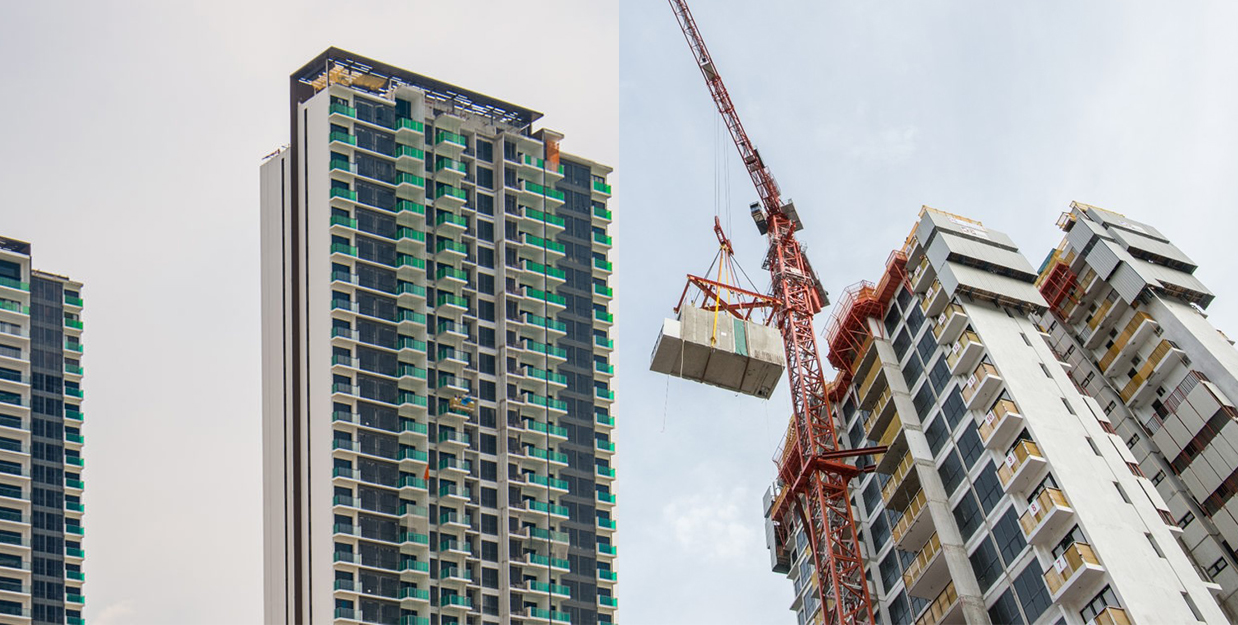
According to Bouygues, going modular and using a central materials and logistics platform was more sustainable, reducing waste onsite by 70% and offsite by around 30%.
And substantially taller buildings are expected to smash that record soon. In the UK, Tide Construction is delivering the College Road residential development in Croydon, which at 49 storeys tall, will be some 5 storeys higher than its previous tallest project, the Ten Degrees tower at George Street, also in Croydon. The contractor is also due to build a 48-storey student accommodation tower at Canary Wharf in London, due to reach 156m tall.
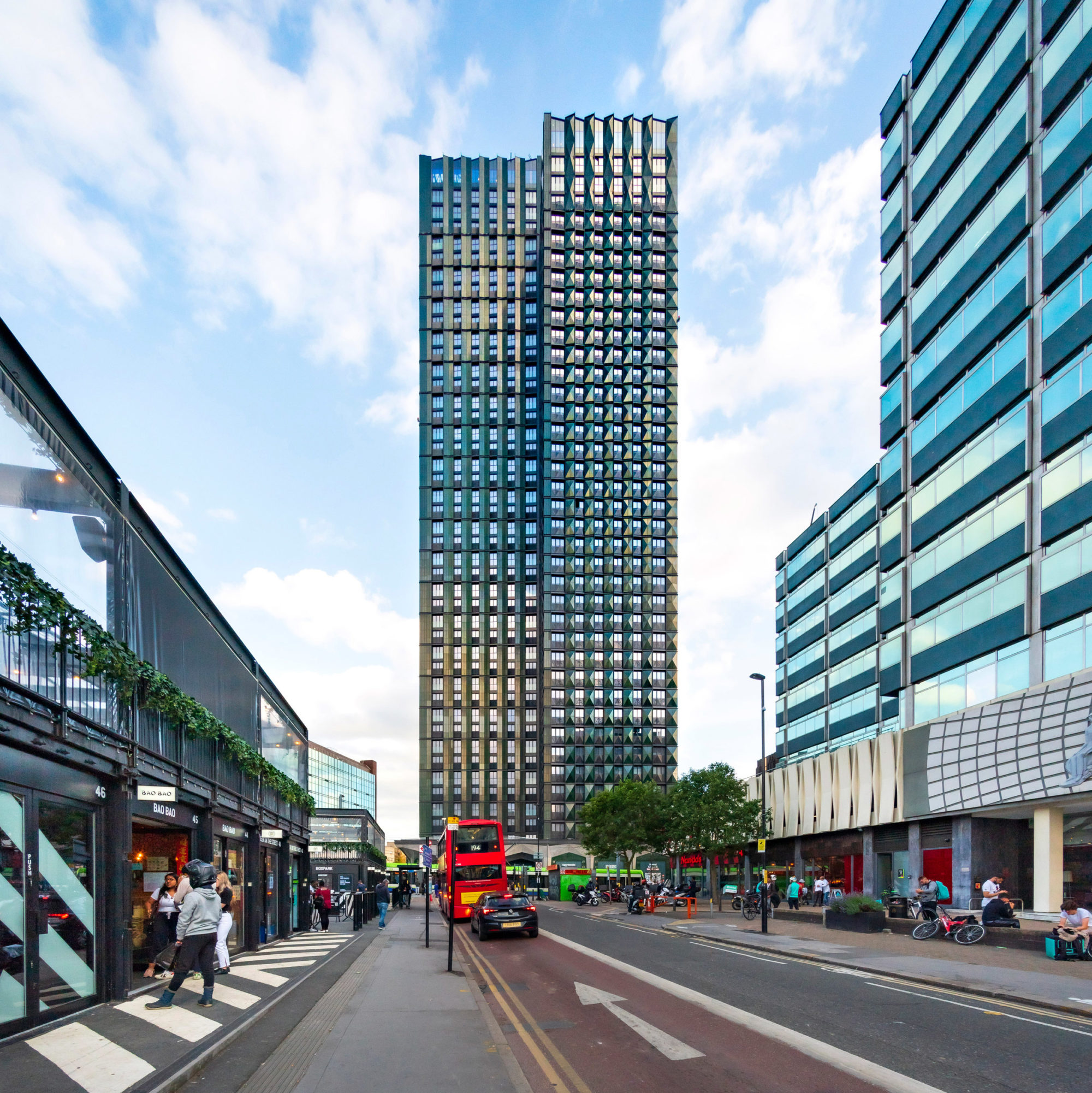
Climate response
As climate change causes sea levels to rise, one architect is asking if zero-carbon modular floating homes could provide a potential solution.
Grimshaw Architects collaborated with Dutch manufacturer Concrete Valley to develop designs for the two-storey Modular Water Dwellings, which would leave the riverside factory in a completed state before being towed on water to their final permanent location.
The homes would be prefabricated from a set of standardised components and include rooftop solar panels and heat exchangers built into base pontoons below the waterline to achieve near-zero energy use.
Free of the constraints of land-based construction, the concept would also tackle the issue of high land values causing a shortage of affordable housing in urban areas. Offsite fabrication using durable and non-corroding components and the associated lack of waste and on-site construction activity would minimise embodied carbon.
Micro living
Housing shortages and soaring property prices have driven a rapid increase in the number of micro homes built in recent years, many of them exploiting modular techniques. The trend for ‘micro living’ apartment blocks started in Asia, but the first example in a western city was the My Micro New York City scheme, now known as Carmel Place, constructed in 2015.
The nine-story, 35,000 sq ft modular building located in Manhattan’s Kips Bay neighbourhood was designed by nArchitects in response to a competition calling for a new model for affordable housing for one- and two-person households.
The 55 units range from 250 sq ft to 370 sq ft in size and feature a kitchen, closet, a combined living and sleeping area and Juliet balcony. To make the project viable, the city had to waive current zoning and density rules that limit apartments to a minimum 400 sq ft.
Back home in the UK, the first micro apartment scheme, located on a constrained site in Mapleton Crescent, Wandsworth, was designed by Metropolitan Workshop for Pocket Living and completed in 2019.
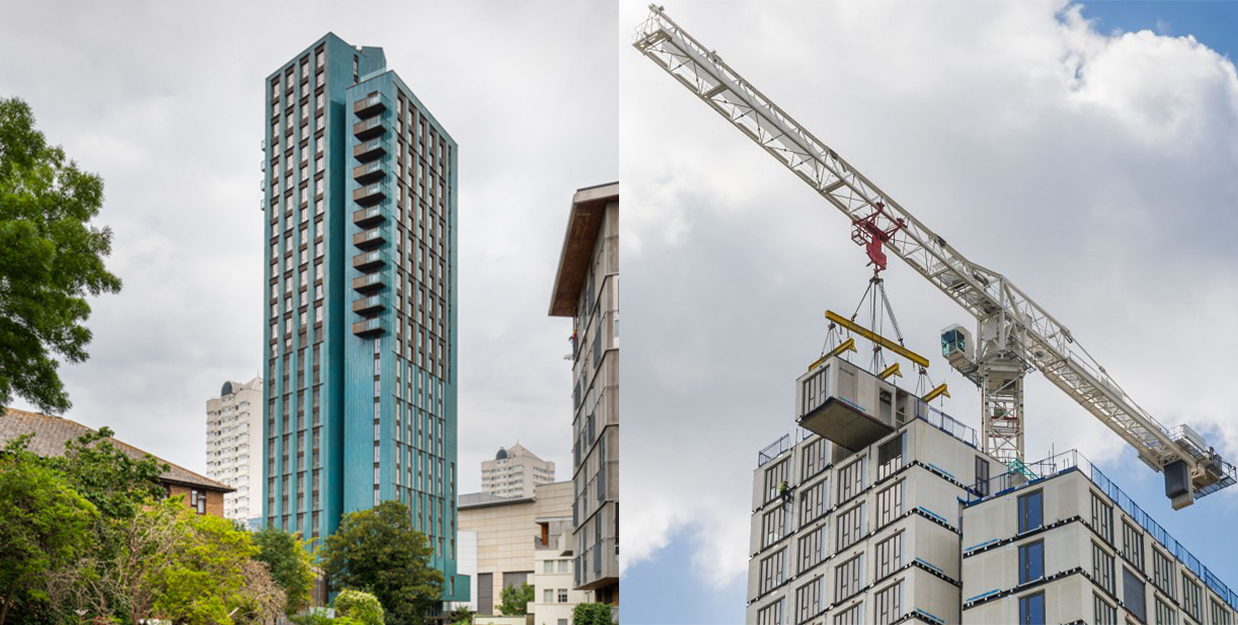
The slender tower features 254 steel-framed modules, which were installed at the impressive rate of one entire floor per day. Volumetric offsite construction was quicker than traditional methods with much less waste and a higher quality finish, speedy erection resulted in far fewer site deliveries and less disruption to neighbours.
Limited land
The high cost and limited availability of land in London has sparked another new blueprint for sustainable urban development based around the idea of grafting modular structures onto the top of existing buildings.
The first ever ‘airspace’ development will see a four-storey, 15-home block constructed on the roof of a 3-storey concrete and brick apartment building on St James’s Road in Southwark.
Developer Skyroom will install the new homes by crane over a period of weeks, eliminating the need for existing residents to vacate their homes.
The structure is based around a proprietary podium system (PPS) designed to support the additional massing on the existing structure like an exoskeleton. A geospatial mapping tool was also created, with funding from Innovate UK, HM Land Registry and Ordnance Survey, to scan parts of a city to reveal roof spaces suitable for conversion before approaching landowners with a proposal.
Skyroom claims constructing above an existing building conserves embodied energy, by reducing the need for new structure, and installing renewable energy sources for both new and existing homes will reduce operational energy.