Intro
A manufacturing-led approach isn’t only great news for productivity and sustainability, it can help resolve the UK’s chronic skills shortage and opens up a plethora of exciting new roles and responsibilities for the next generation of digital-savvy construction workers…
The construction sector is facing a crippling skills shortage. The latest Construction Skills Network report estimates that an extra 225,000 construction workers may be needed by 2027 to meet expected output - an increase of just under 45,000 per year over the next 5 years - with “substantial recruitment and training challenges” if that target is to be met.
The UK government has estimated that, based on current levels of new entrants, the sector is likely to see a 20% to 25% decline in the workforce within a decade, which comes on the back of years of low productivity growth in the sector. Its target to build 300,000 new homes a year from 2025 to address the housing crisis is already floundering with worse ahead if current employment trends continue. The transition to offsite and with it the adoption of a standardised, production-line approach to delivering buildings can not only increase productivity and efficiency, it can reduce the impact of the declining workforce. Moving jobs into a factory environment typically ensures more predictable employment levels and lessens the need for workers to move between different sites. As Gleeds points out in a recent report on offsite, greater reliance on digital working can help attract ‘new entrants to the industry and challenge traditional perceptions.’
Transition
Of course a mainstream transition to a manufacturing mindset will be hard won in a sector known for being slow to innovate. It demands a reassessment of traditional roles and processes, changes to knowledge and the people involved, and the extent and timing of collaboration. It means greater reliance on BIM workflows and digital modelling and verification tools to automate design. Against this background, “individuals with qualifications in traditional industry disciplines will need to acquire new skills and change their behaviours,” the RIBA states in its updated DfMA Overlay to the RIBA Plan of Work.
At the project team level, it could demand the creation of new roles and changing how collaboration is organised. At an organisational level, the RIBA says it could mean a shift to either vertical integration, from project feasibility through to asset management, or horizontal integration, putting all design disciplines under one roof, or both. Another option is longitudinal integration, whereby feedback loops enable continual improvement to deliver better value over time.
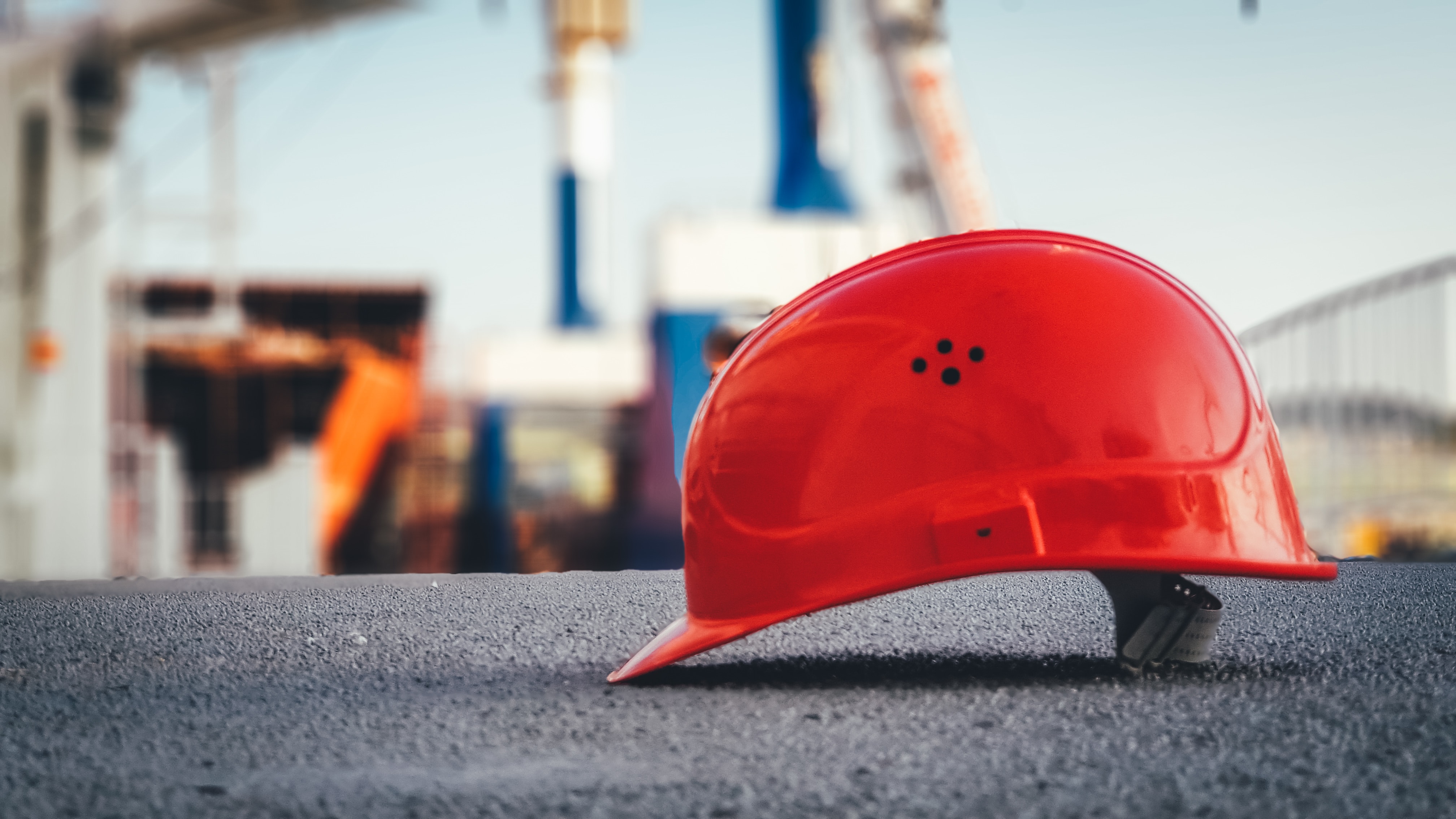
The RIBA states that the organisational transition to MMC is “an evolution of business as usual” rather than a wholesale revolution. That said, a production-line approach to building largely sidesteps the need for traditional construction skills that have created endemic labour shortages. A new report on modular’s role in solving the housing crisis, by trade association Make UK Modular, highlights that over 65% of modular producers’ workforces are in assembly line roles with no or few entry requirements and only 10 to 15% of workers in construction trades, in most cases.
This frees projects from traditional labour constraints and removes many of the barriers that limit entry into traditional construction. More compartmentalised assembly line work, with each worker assigned a specific task, makes it “quicker and easier for workers to learn to do their jobs” and “easier for employers to carry out in- house training,” the report states. Furthermore, optimising processes opens up the workforce to different population demographics. In modular, around 16% of the workforce are female, versus just 1% of on-site workers in traditional construction.
Modular
Modular is a very different take on design and build, placing a stronger emphasis on the liaison between manufacturers, architects and the wider supply chain. For architects that means maintaining a constant line of communication throughout design, fabrication and beyond. It also places a stronger emphasis on coordinating models and documentation in BIM to align with fabrication processes, whilst adhering to timelines set out in the DfMA Overlay to the RIBA Plan of Work. Indeed, digital technology is central to the creation of next-generation MMC schemes and to how schemes are designed, costed and built.
The government’s newly updated Construction Playbook references this as essential to the advancement of MMC and a necessary move away from traditional construction’s reliance on inefficient systems and manual processes considered detrimental to business performance. Digital skills relevant to MMC encompass a plethora of areas and activities and continue to evolving all the time. Computer coding skills are increasingly needed to enable design automation for configuration, optimisation and customisation, including the algorithms that underpin these processes.
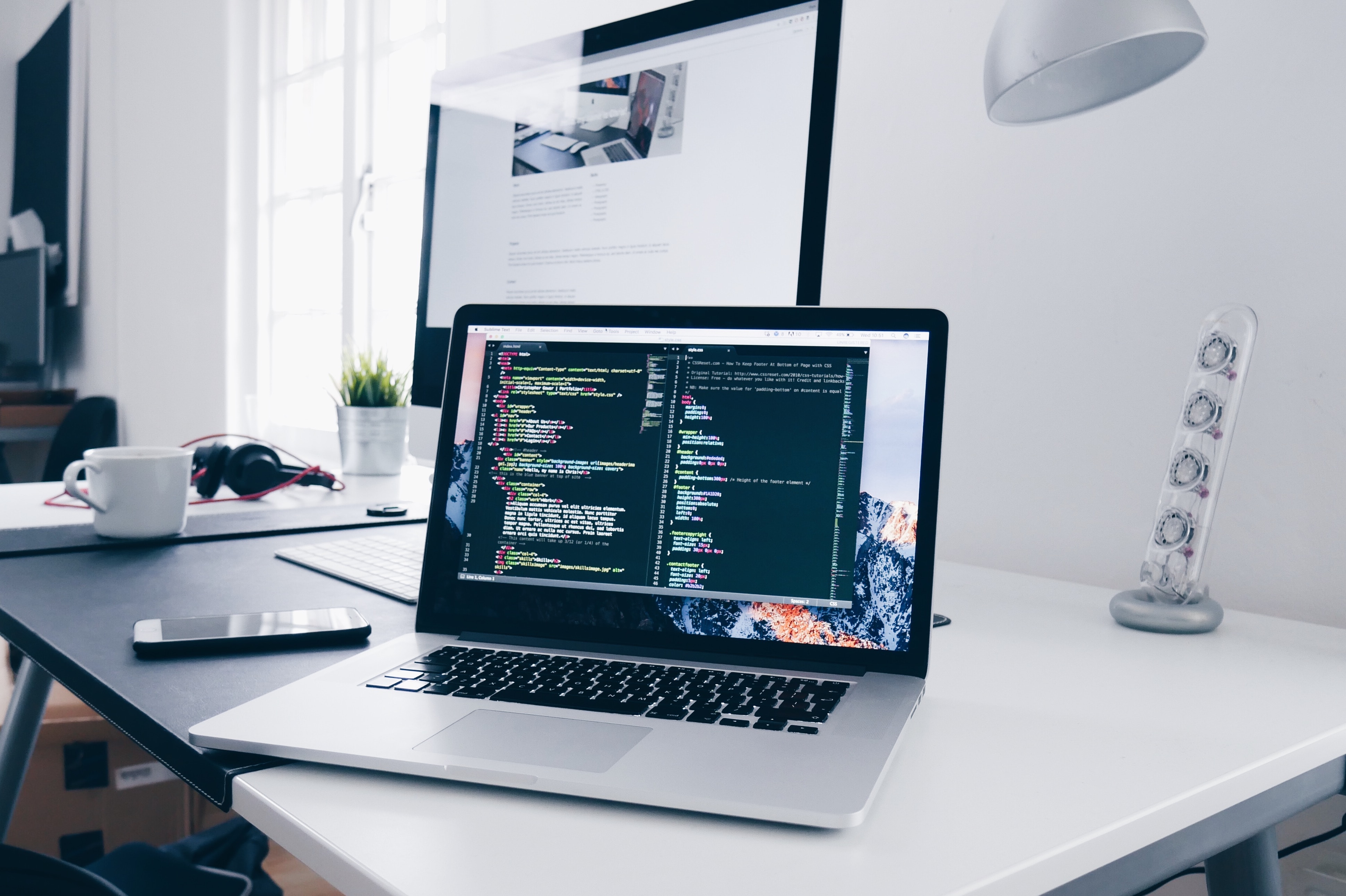
Skills in information management are already widely used across the industry for BIM, but there is a need for a whole raft of new roles in data management, from cyber security specialists and data architects to process modellers.
Skills in the processes and tools (excluding KOPE of course) needed for MMC optioneering “are currently patchy across the industry, with some pockets of excellence” the RIBA states in its DfMA overlay. It therefore recommends that the role of MMC Adviser, responsible for coordinating optioneering process and assessing which construction method or system best suits desired project outcomes, is taken mainstream. This role could be undertaken by the architect, if they have the necessary knowledge, by a specialist consultant, or as an inhouse function by the client.
Move to MMC
The move into MMC will hit a wall if the industry can’t upscale its knowledge of manufacturing and properly anticipate fabricators’ highly influential cost drivers. As a result, manufacturers will need to make more of this information available, and project teams will need to understand how to exploit it to optimise value. This is directly an area of focus we have taken on at KOPE. The ability to offer this information in the right ways for each stakeholder will be crucial.
Engineers typically take on more of a leading role in MMC builds, advising on technical aspects and understanding how innovation can be harnessed to overcome challenges and create effective design solutions. Related to this, ‘integrator’ roles - essentially a systems engineering function - may become more common as manufacturing expertise is added into MMC projects, to help deal with unforeseen consequences and provide active management and coordination. How well the sector is able to respond to the digital upskilling challenge will take shape over the coming years as MMC is embedded deeper into construction and procurement. Designers, consultants and contractors will need to engage in programmes that develop future talent and invest to retrain traditional construction workers in new roles.
The creation of new Construction Academies as part of the Government’s National Retraining Scheme and work by organisations like Sharing in Growth, which has an established track record for delivering business transformation within UK manufacturing and engineering companies, will provide valuable support.
There’s still work to be done in raising the maturity of the supply chain to deliver using MMC, and to foster collaboration and move away from traditional transactional, adversarial contractual relationships. At KOPE, we hope to provide the digital platform underpinning some of these industry changes.