Building a modular home is fundamentally different to constructing one in the traditional way. The level of complexity and accuracy required alongside rigorous quality control requires a particular approach. Every dimension, tolerance, and offset needs to be precise and fully-coordinated meaning significant information is required to articulate each module in fine detail. The creation of this content, its coordination and its implementation required a lot of time and manual work.
Before the development of ilkeX, the process of taking the early designs and creating the fabrication and assembly content took a team of 8 people within ilke Homes a period of 3 months to produce. This included 4000 drawings required to manufacture a home using multiple design tools, while also relying on an interoperability workflow between software that simply doesn’t exist to the level ilke Homes require. On top of this considerable amount of work, the introduction of robotics and machinery on the factory floor left little room for error and manual intervention.
As ilke Homes strive to create the best homes available in the UK and with a new product line on the horizon, the goal was to automate the production of all information relating to linings, fixings, framing, all openings in steel, plasterboard, sheathing board etc, then coordinate within a 2mm tolerance to allow for a full product range refresh in a single phase rather than one at a time.

When matterlab and ilke Homes began to work together in 2020, they challenged themselves with finding a solution to the problem above by leveraging technology and automation to massively accelerate product revision cycle time, reduce errors, enable full virtual prototyping, integrate BOM & ERP, and digitally transform the end-to-end process.
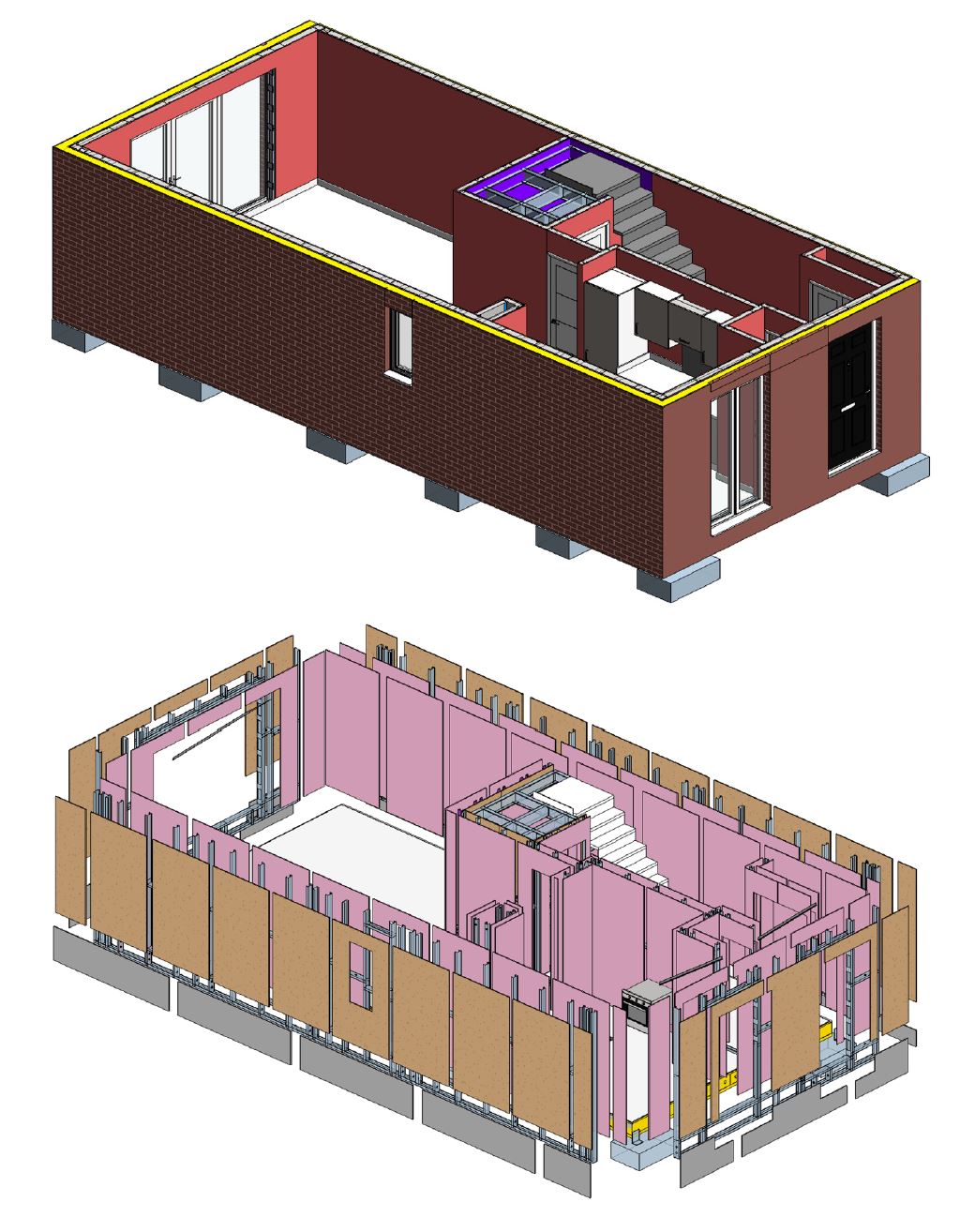
‘Project Refresh’ was an internal initiative at ilke Homes to update the existing product range taking on board client feedback, harmonising chassis designs (reducing modules, yet increasing house-types) and enabling faster and lower cost manufacturing & maintenance of ilke Homes zero carbon product ‘ilke ZERO’.
Based on the new house types, the concept of ilkeX was born; to “codify” the wealth of manufacturing knowledge in the ilke Homes team by developing the underlying logic built on relationships between components. If the design of an element changes, how does that effect its neighbours within the module? A moved window position will mean different cuts and fixings for all boarding in its vicinity as an example.
The process of offering up the internal experience and knowledge of ilke Homes to matterlab involved a year of workshops, meetings and intense collaboration. By taking the drivers for component placement and fabrication within the modules and converting that to clearly defined, but interrelated mathematical rules, an automated solution was developed. ilkeX works by taking a model authored in design software such as Autodesk Revit or Inventor and converting the monolithic pieces such as walls, into their fabricated parts. Not only this, but all fixings and penetrations are instantly aligned, accurately producing the required outputs for the factory floor. ilkeX understands the physical constraints of different materials, the methodology developed by ilke Homes and the technical requirements of the factory floor.
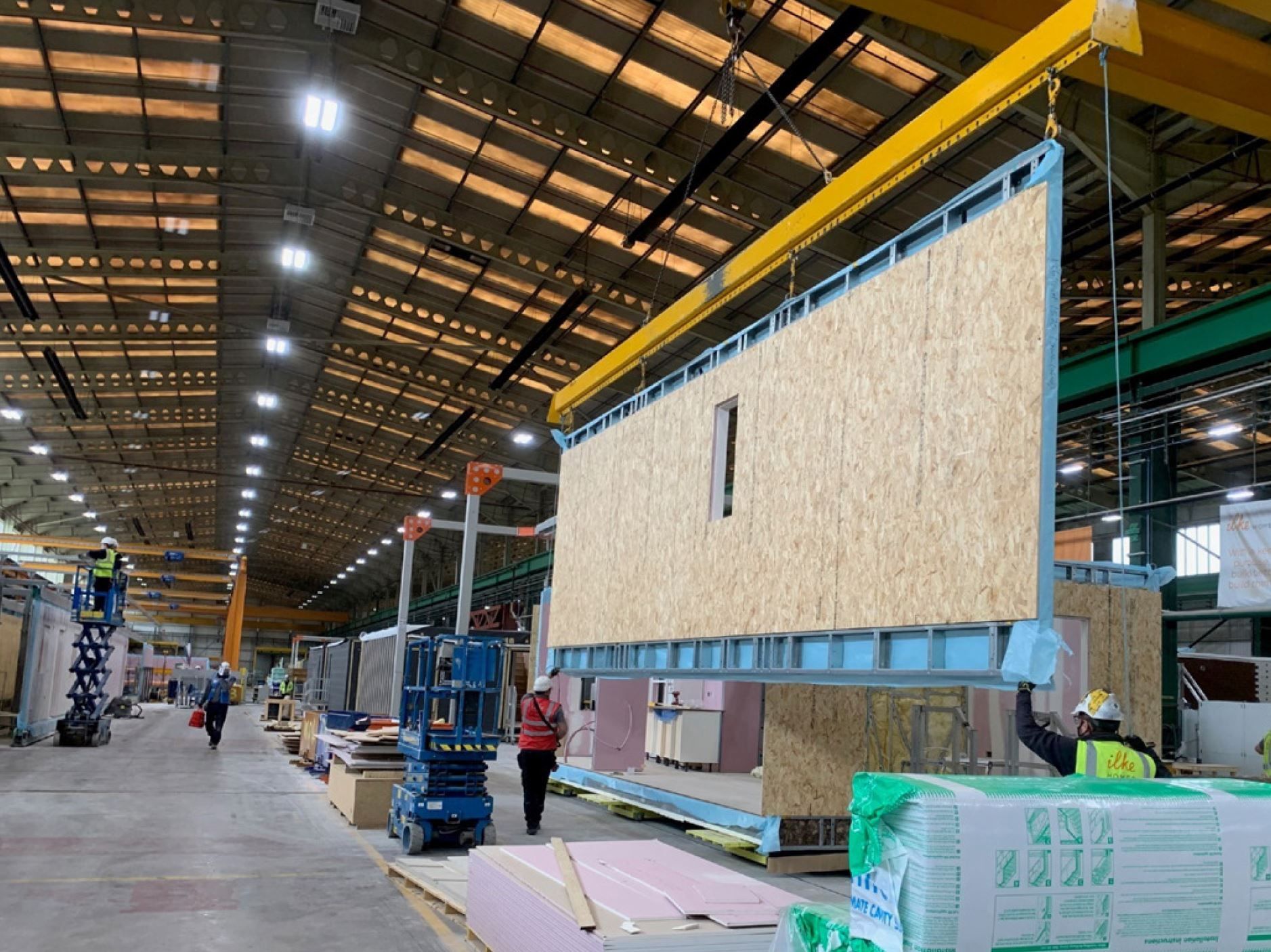
Whilst developing ilkeX, matterlab and ilke Homes went through a period of virtual prototyping. The software automated the creation of a complete digital replication of the entire module including every piece of boarding, insulation and fixings across all walls, ceilings, and floors. To fully deliver the extreme time savings possible, ilke Homes needed to automate the outputs required by the factory floor. Automating this allowed for a fluidity in design changes and ensured the output was free from human error. After clearly defining what needed to be presented on each drawing, matterlab were able to develop a framework for the entire fabrication set – all drawings, schedules and machining files, and produce them automatically within minutes.
If any design changes were required, which is always likely when building houses across different councils and authorities, the software could be rerun to update the model and drawings accordingly. No lengthy reworking of drawings, no delays to ilke Homes’ customers.
This process enabled matterlab to develop a framework to take construction knowledge and requirements and turn them into logic-based rules. The framework for wall panels could be applied to floors simply using different inputs. This holistic approach, coupled with advanced computational design processes allowed ilke Homes to explore the automation of all stages of modular fabrication.
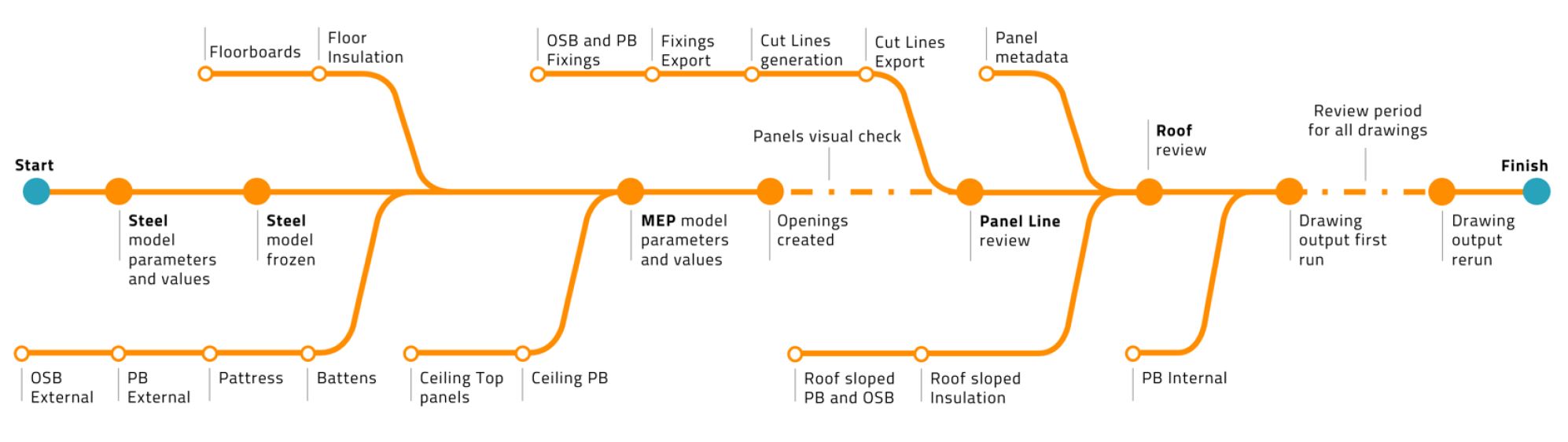
In June of 2021, a year after beginning this collaboration, modules designed and documented entirely from the software were built on the factory floor with precision engineering and automated manufacturing. This introduced huge financial savings throughout ilke Homes and reduced errors in the overall process, reducing downtime on the factory floor which can costs upwards of £50k/day.
While ilkeX is centralised around the internal expertise and quality of modular construction at ilke Homes, it became clear that aspects of the tool could be developed in a wider initiative for any off-site construction methods. This led to the beginnings of KOPE. At its core, matterlab hope that KOPE allows more companies in the construction industry to benefit from the same precise level of automation. With KOPE, matterlab are building a platform that allows for the application of systems and products from the supply chain, at any stage to your design files, giving extensive clarity to decision making at earlier points when testing ideas is less costly, less damaging to the success of a project.
As matterlab and ilke Homes further evolve ilkeX, they remain committed to using their experience and technology to ensure the homes of the future are more comfortable, affordable, and sustainable. This will be driven by the next phase which aims to optimize all material waste across ilke Homes entire portfolio. Material that would normally be cut and discarded on Module A may be a perfect fit for Module B. By allowing the design teams to see the fabrication impacts as they design new homes, ilke Homes expect to have major waste reductions across all of their manufacturing processes.
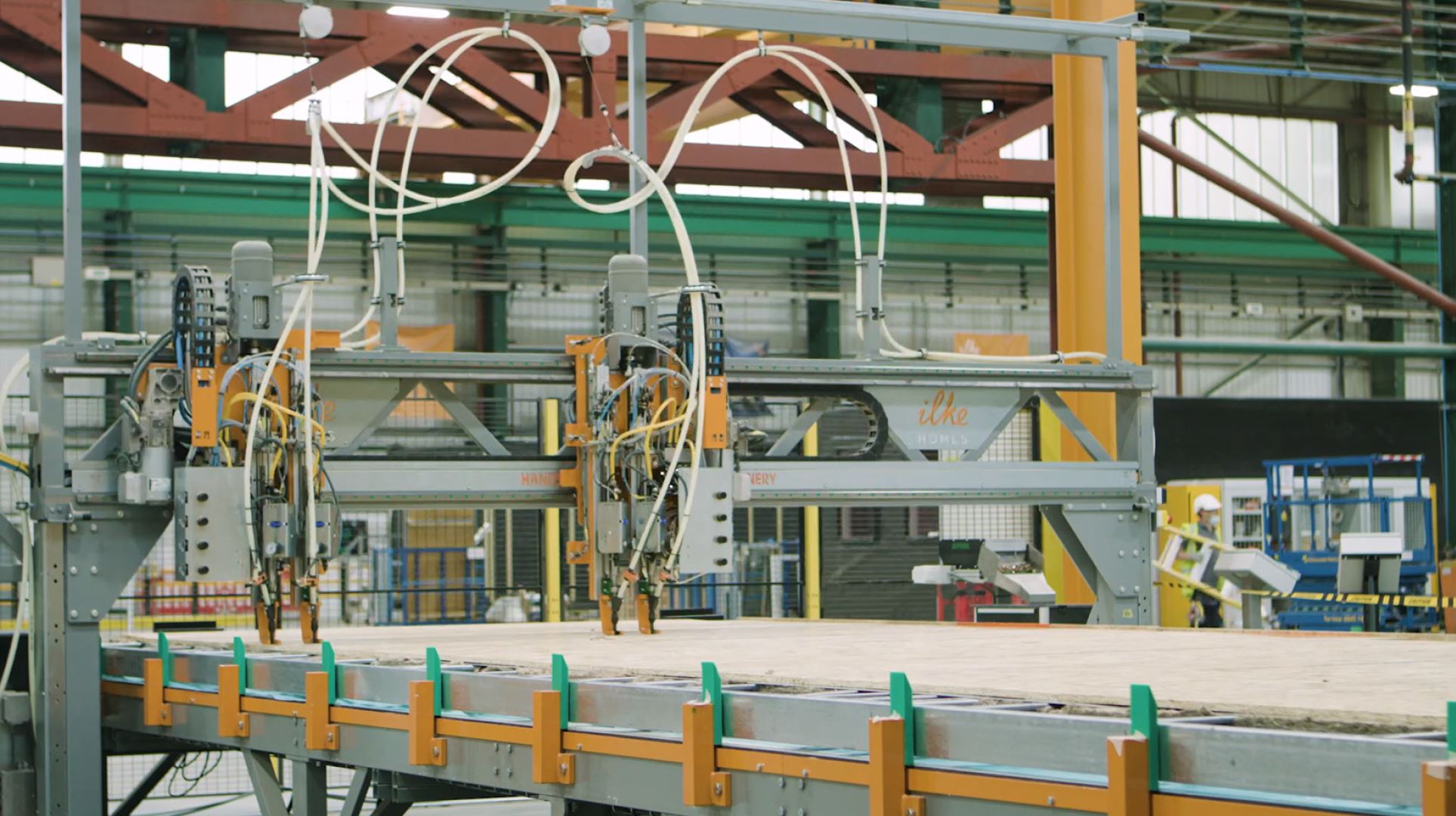