The Status Quo of Quantity Take Off
High-quality quantity take-offs traditionally take time, often requiring manual methods to interpret designs and calculate results. Estimators must painstakingly interpret complex designs and perform tedious calculations, frequently juggling disconnected spreadsheets and manual data entry. This entire process is inherently fragile – prone to inconsistencies between team members, costly human errors, and frustrating rework cycles, especially when designs inevitably change. These flaws introduce significant risk, obscure true project costs until it's too late, and can directly lead to damaging budget blowouts or lost competitive bids.
KOPE is changing this, allowing companies to generate instant take-offs, test and compare different options, and optimize layouts to discover cost-effective solutions – achieving significant results in speed, cost, and sustainability. We want you to win more work by quickly understanding costs and project feasibility.
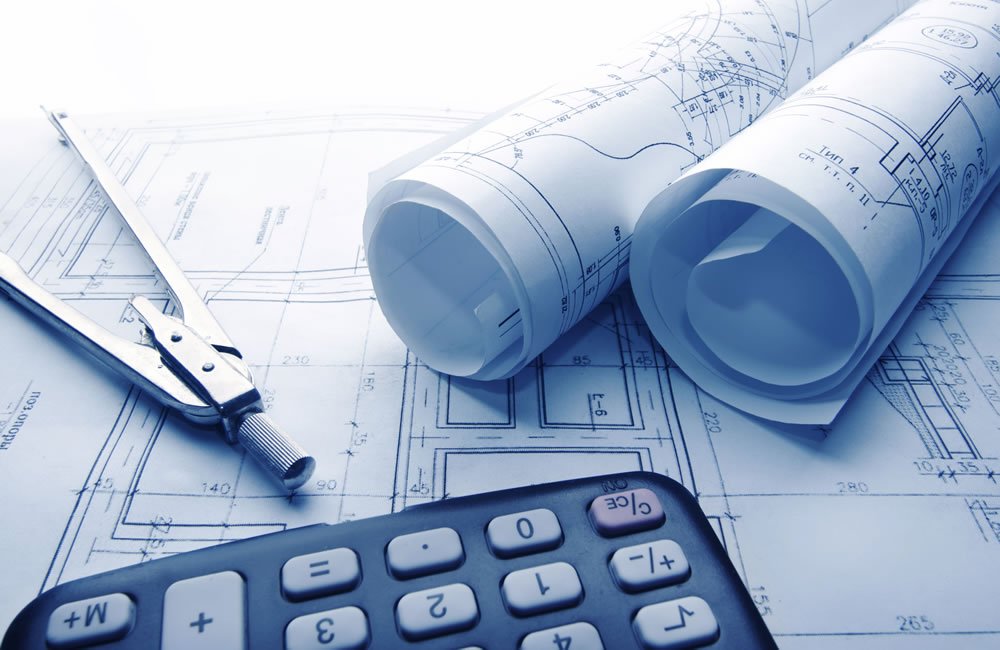
QTO: The KOPE way
KOPE transforms the QTO process by enabling you to generate fast, accurate take-offs within an easy-to-use 3D environment. KOPE provides early insights into project suitability and the feasibility of using specific manufactured systems. Will a certain product be a sensible solution cost-wise? We let you find out, in seconds.
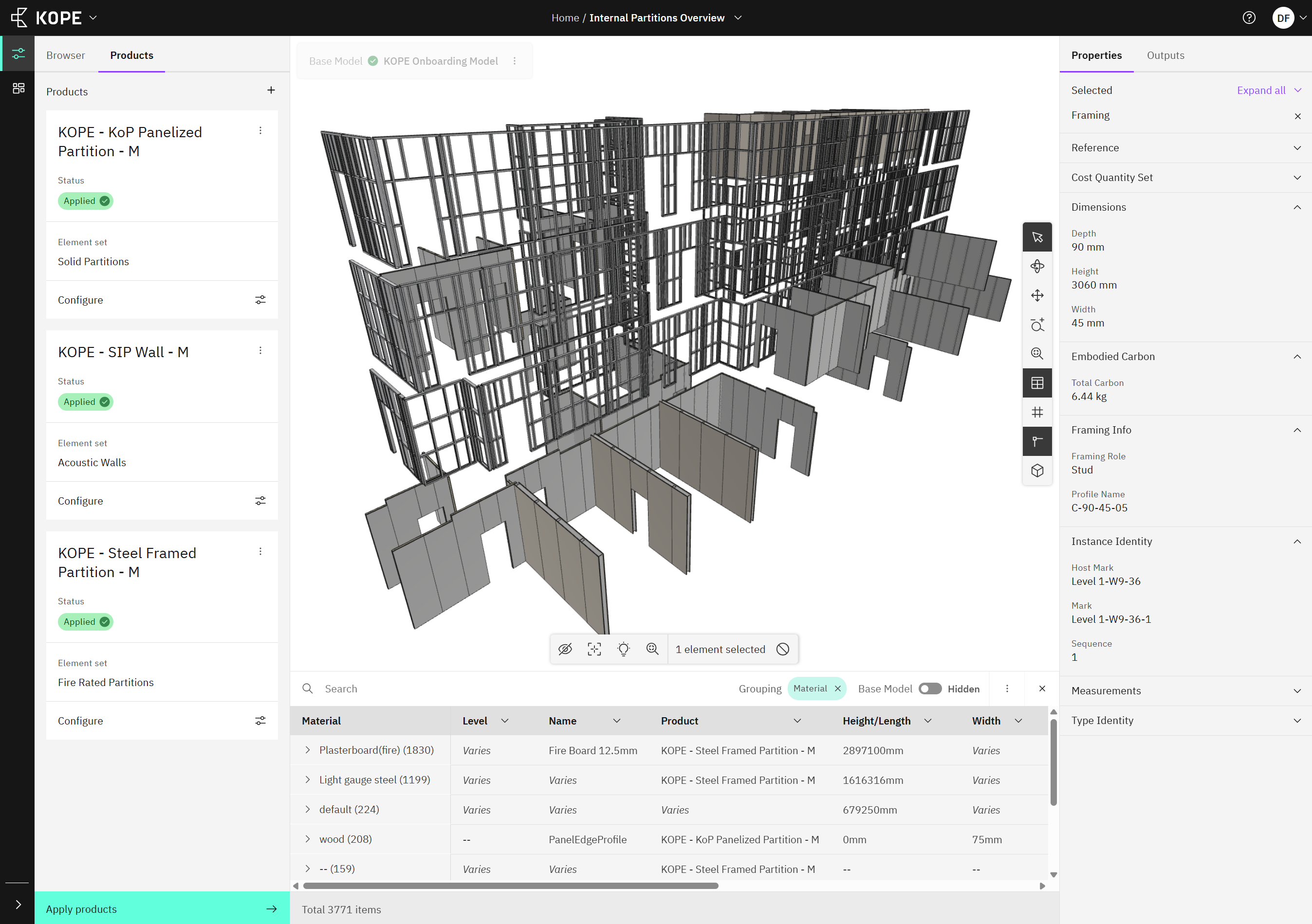
KOPE changes QTO through three key drivers:
Speed: KOPE delivers results incredibly fast allowing manufacturers like Addazu, for example, to reduce their proprietary system configuration time by 100x. Crucially, this speed means you can reconfigure alternates and explore different options rapidly. It empowers any team member, whether a trained estimator or someone in sales/BD, to generate accurate take-offs quickly, democratizing the process. As Kelly Pickering, Founder of Addazu, puts it: "By implementing the KOPE software, Addazu can conduct real-time design iteration meetings [and] produce detailed estimates in minutes..."
Automation: KOPE takes care of previously manual tasks. It reads a design model, applies selected products directly to it based on requirements, optimizes the placement, and automatically generates associated quantities and costs, crucial for deploying sophisticated kit-of-parts systems efficiently.
Accuracy & Quality: Embedding precise system requirements and production constraints allows KOPE to drastically improve accuracy and reduce errors. Consistency is built-in, as embedded company standards ensure reliable results regardless of the user. KOPE's rapid, rule-based engine also instantly flags constructability issues (problem areas, non-compliant placements), offering risk feedback in seconds, not days. It even reveals efficient, non-obvious solutions missed manually – like identifying a waste-cutting unconventional board size for British Gypsum. Ultimately, KOPE generates quantities and costs rooted in buildable reality, powering competitive bids based on fact.
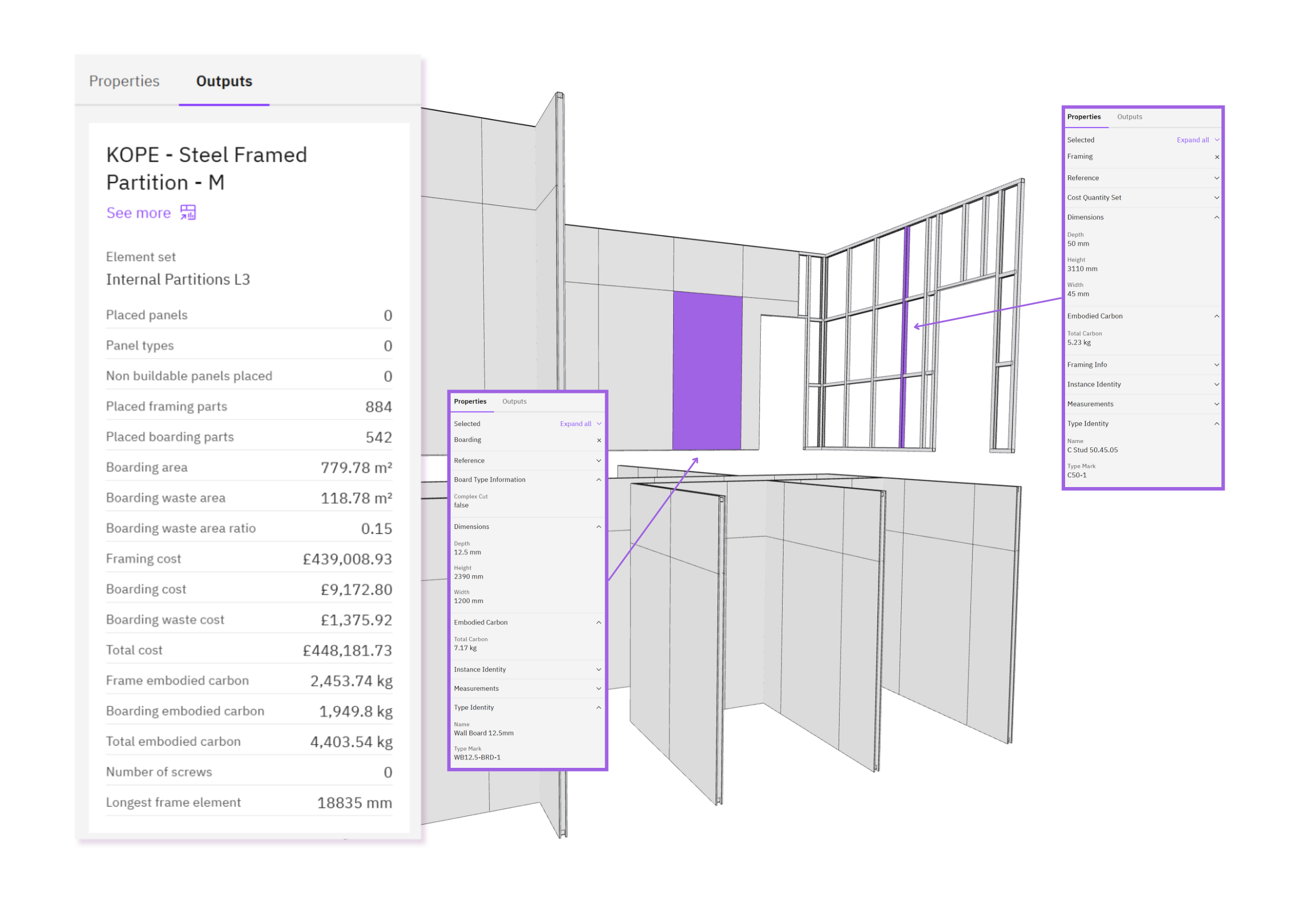
Let's see how KOPE does this...
First, we use real-world building products defined by their manufacturer, or you can add your own proprietary product or system to KOPE such as when Lada Build did just that, allowing them to embed their unique system logic. These KOPE digital assets come complete with spec data, configuration logic, and application rules embedded within. This enables fast, consistent take-offs and rapid updates when revisions occur. You can leverage pricing data from the product supplier or establish your own project-specific costs through KOPE's cost manager.
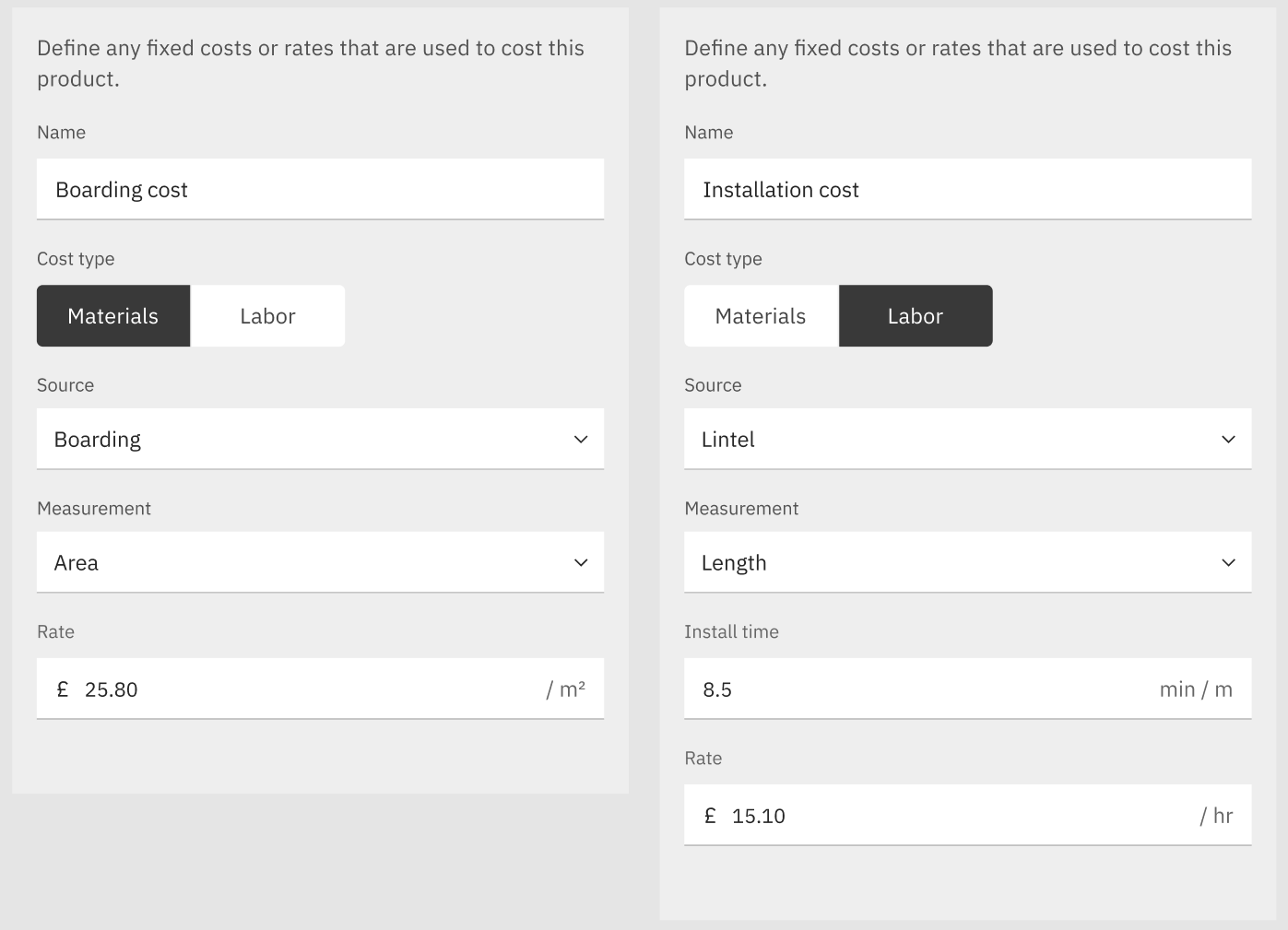
KOPE automatically configures and places your chosen products onto the relevant parts of your design model according to their embedded rules and your requirements, giving you immediate feedback in the 3D viewer and data table. You control the cost outputs to suit how you price jobs. If the initial result needs refinement, you can easily make tweaks.
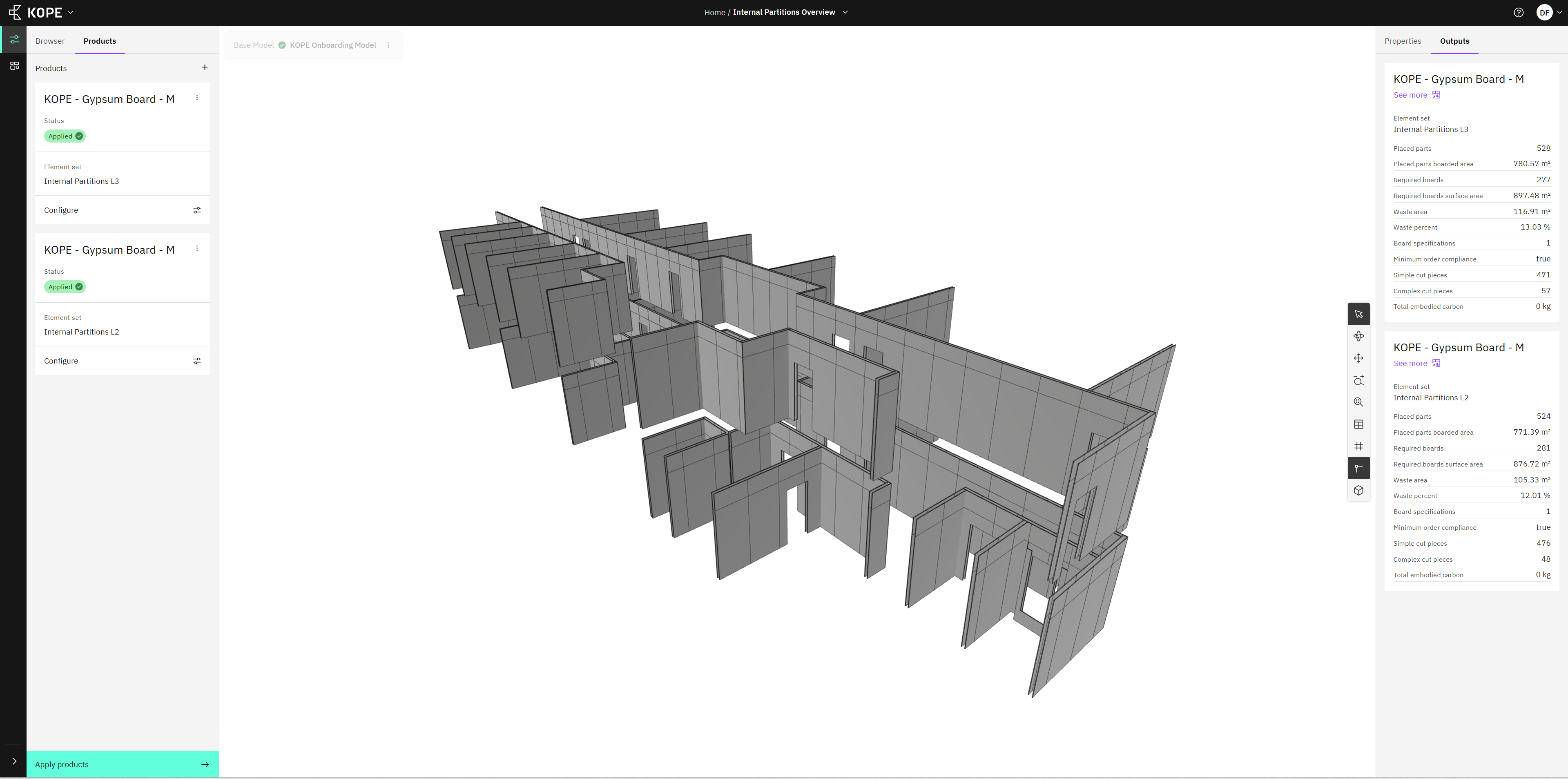
The Configure panel allows quick adjustments, such as exploration of lower-carbon configurations, letting you rapidly test variations at speed. Because of this rapid iteration capability, teams can engage in real-time design meetings, as experienced by Addazu, allowing teams to test and retest multiple scenarios quickly, arriving at take-offs that perfectly suit cost and sustainability needs. You can also inspect individual placed elements to understand their specific properties for further validation.
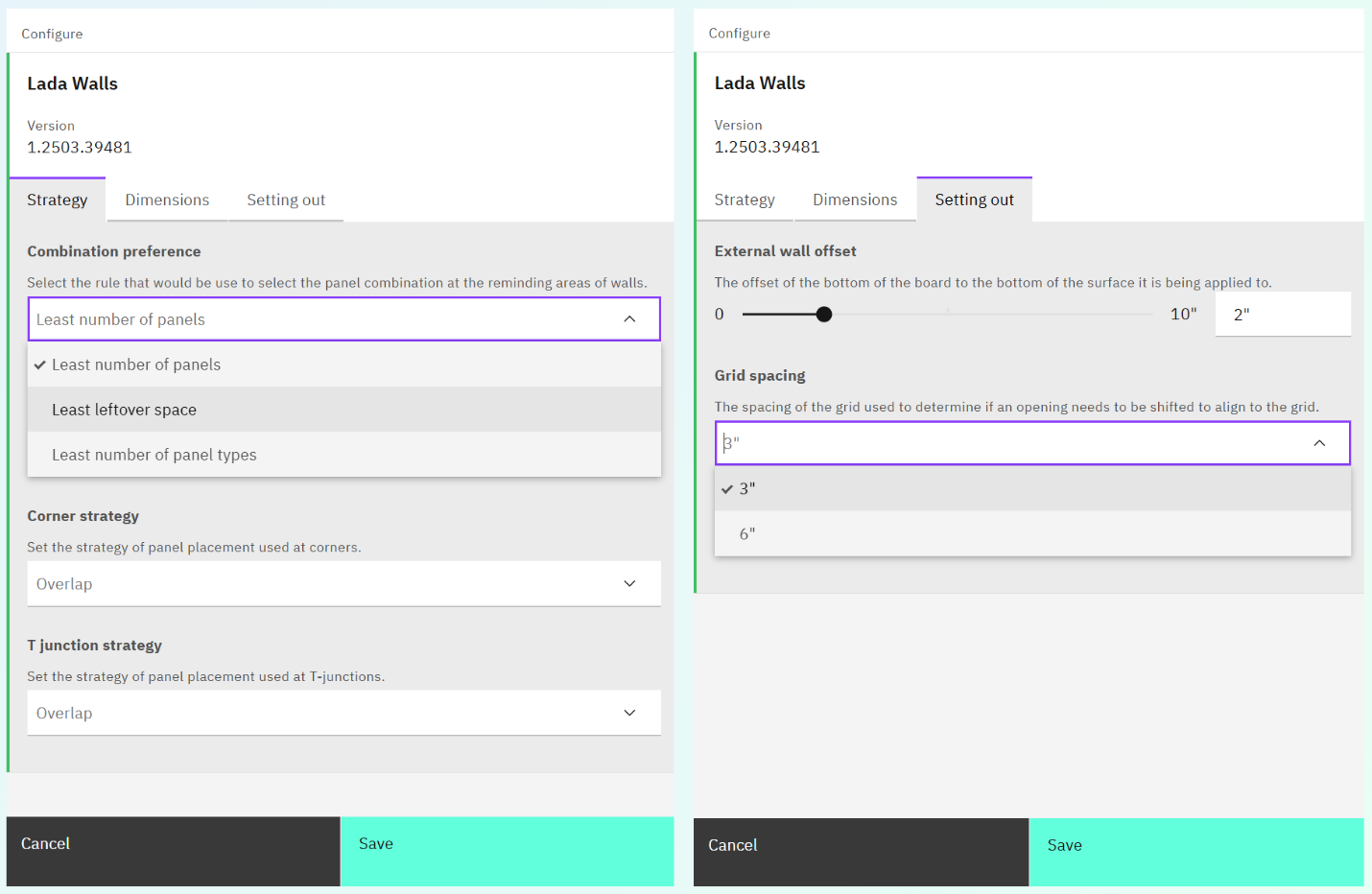
Now, with content placed directly within the project context, you can dive into automatically-generated metrics via output cards for a birds-eye view of the options created. That includes quantities, costs, standardization metrics, waste calculations, and crucial embodied carbon data related to your specific application, making sustainability a measurable part of the QTO process. If the results aren't quite right, simply tweak the configuration and rerun in seconds – ensuring carbon-conscious decisions are just as accessible as cost-driven ones.
.png)
KOPE’s data table allows easy viewing of all this QTO data, making it simple to understand the elements creating your take-off and pricing plan and provides a quick way to export comprehensive data (including cost, quantities, standardization, waste, and carbon) for seamless handoff to analytics platforms like PowerBI. This allows you to build interactive dashboards and reports without additional data prep, ensuring continuity between design decisions and live price tracking.
With KOPE, you can then efficiently analyze results. The platform empowers you to compare outcomes effectively, assessing different products or adjusted configurations with minimal reworking. Then leverage powerful optimization tools to find the best solution based on your goals (e.g., minimize cost, maximize standardization, reduce carbon). Want to reduce custom parts? Just run an Optimization.
Finally, download your data outputs – such as schedules, Bills of Quantities, cost reports, and updated 3D models – ready for tendering, manufacturing, or further design stages, ensuring accurate data supports your cost management.
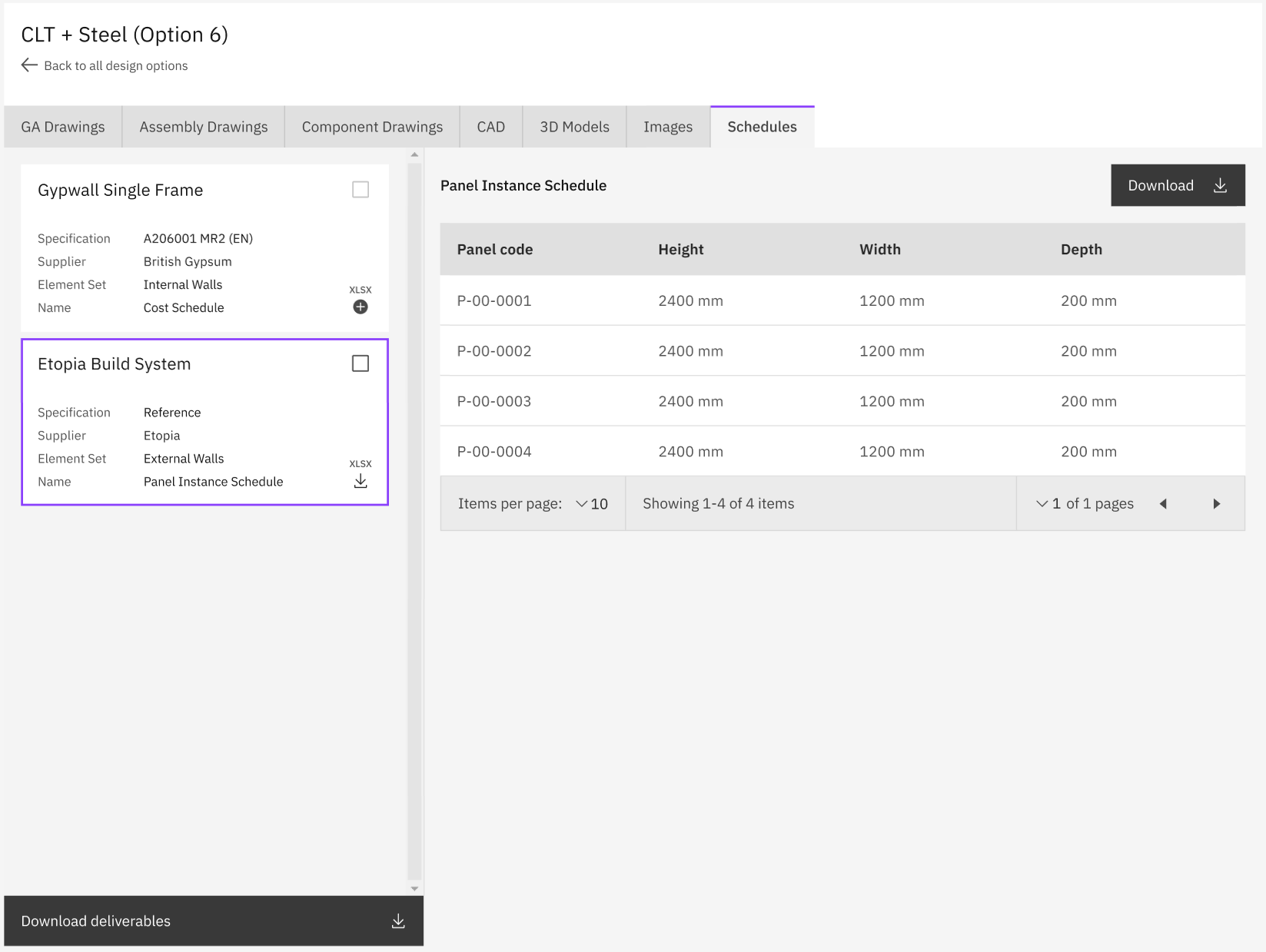
KOPE: Smarter quantification with faster results
Going from a project model to accurate costing in minutes, KOPE brings you the future of the QTO process by applying real-world products directly into your designs, all connected to your cost/pricing data. Instantly unlock crucial insights that go far beyond basic take-offs; analyze cost, waste, embodied carbon, constructability, and project suitability/compatibility in real-time. Effortlessly compare scenarios and leverage advanced optimization tools to pinpoint the best design solutions for your goals, driving transformative results like 100x speed improvements, significant operational savings, and dramatic waste reductions. KOPE then streamlines your workflow by automatically generating key outputs like BoQs, schedules, and models, integrating seamlessly with your existing workflows and analytics tools.
Experience the speed and intelligence of KOPE to truly transform your project quantification.